Scope of Project
This project combines new technology with an older vehicle to create a high-performance, custom-built turbocharged BMW E36 M3. I started from a stock chassis and integrated all systems and components to achieve a unique blend of power, performance, and aesthetics. The primary goal is to create a street-legal, track-capable vehicle that reflects my vision, passion, and engineering expertise.
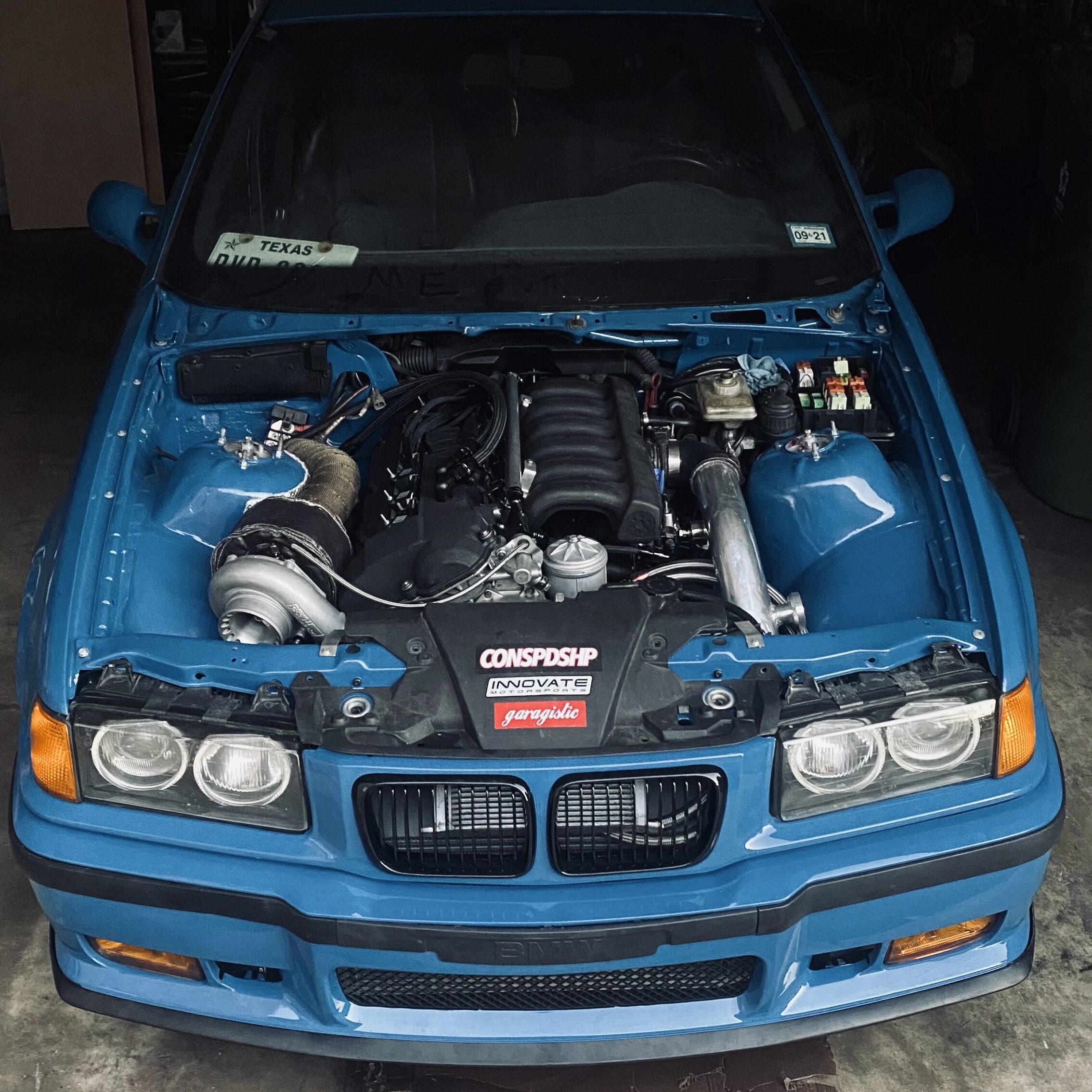
Electronics
Electronic Control Unit (ECU)
The mind of a car is its ECU. It takes inputs from various sensors on the engine, analyzes them, and outputs signals to tell the engine what to do. I chose the Link G4X Standalone ECU because of its capacity to incorporate multiple safeguards to ensure engine health, its capability to seamlessly integrate additional sensors and outputs, and its user-friendly interface.
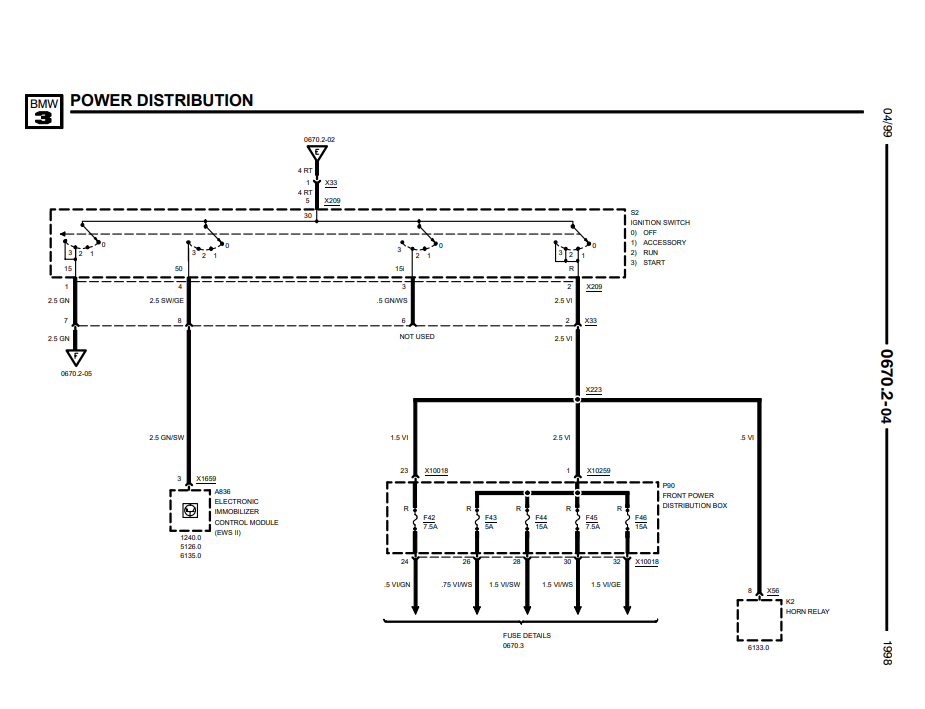
Wiring Harness
The wiring harness facilitates communication between the ECU, the engine, and the vehicle’s internal systems. I designed a custom wiring harness to enable the integration of new sensors that were not originally present in the factory setup. This allowed me to monitor essential engine data, which could be utilized both for enhancing the car’s performance and ensuring optimal engine health. In addition to the OEM sensors, I integrated supplementary sensors to monitor fuel pressure, ethanol content, manifold pressure, oil pressure, air/fuel ratio, and a fast-response intake air temperature sensor. Furthermore, I incorporated new output channels for a boost controller, extra cooling fans, and a shift light.
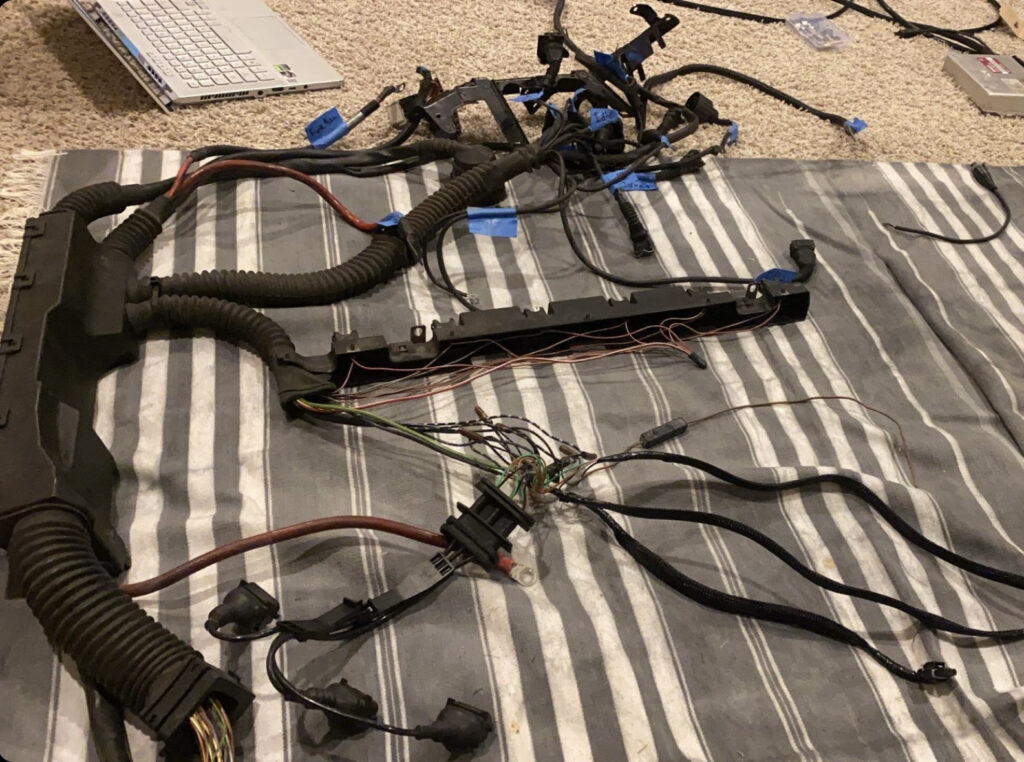
Software Configuration
At this stage, the car has all the essential hardware and components required for operation. Nevertheless, it lacks the necessary instructions for effectively utilizing the incoming data from various inputs. It must also determine the appropriate output values to control the engine components. The software setup encompasses tasks such as establishing the optimal injector duty cycle to ensure a balanced air/fuel ratio during idling, specifying the timing for the activation of coil packs, generating data tables dictating the activation of cooling fans, and fine-tuning PID values to achieve a smooth idle. Additionally, I integrated numerous fail-safe mechanisms at to safeguard the engine when sensor input values deviate beyond specified thresholds.
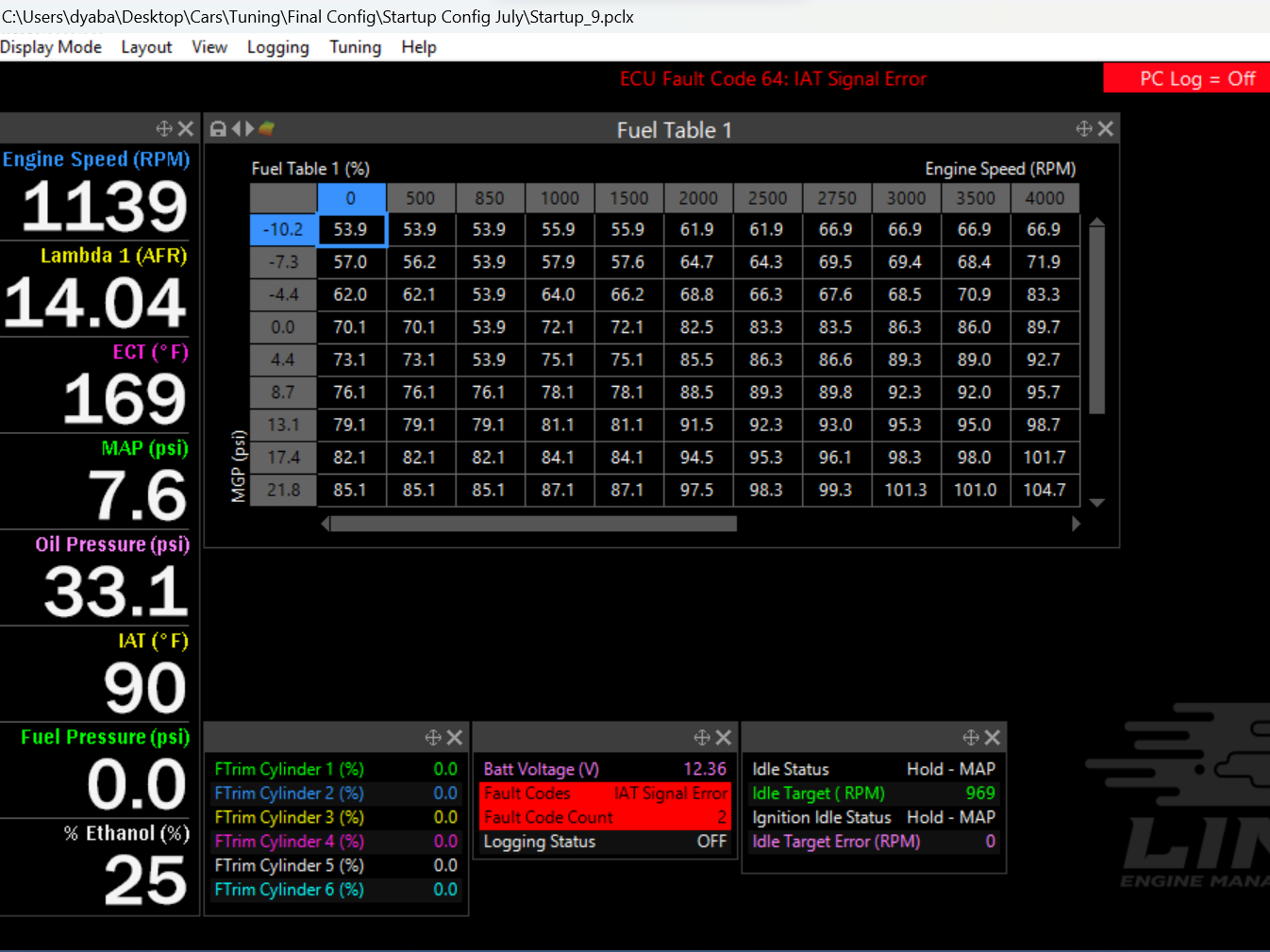
Engine
Block
I opted for an M52B28 Block that underwent machine work to enlarge the bore from 84mm to 84.5mm, in order to accommodate the larger, forged aftermarket pistons. It’s worth noting that M3 engines are equipped with bore sizes exceeding 86mm, but those larger dimensions entail thinner cylinder walls that can be susceptible to cracking when surpassing 700whp.
In my approach, I selected the 2.8L crankshaft with a shorter stroke length. This choice was rooted in its capacity to achieve higher RPMs compared to a 3.0L or 3.2L crankshaft. Additionally, utilizing a 2.8L crankshaft translates to reduced cylinder pressures, increasing the longevity and reliability of the engine.
Regarding the pistons, I decided to go with a compression ratio of 9.3:1. This particular ratio strikes a favorable balance for a street-oriented vehicle designed to run on both 93 Octane gasoline and E-85 (85% ethanol) fuel. It’s important to consider that a higher compression ratio heightens the risk of engine knock when paired with lower Octane fuels.
To reinforce the engine’s integrity, I adopted the well-proven 135mm Eagle H-beam Rods. These rods have established their reliability across numerous high-horsepower builds. These rods exhibit remarkable durability and are rarely identified as the weak link in these engine setups.
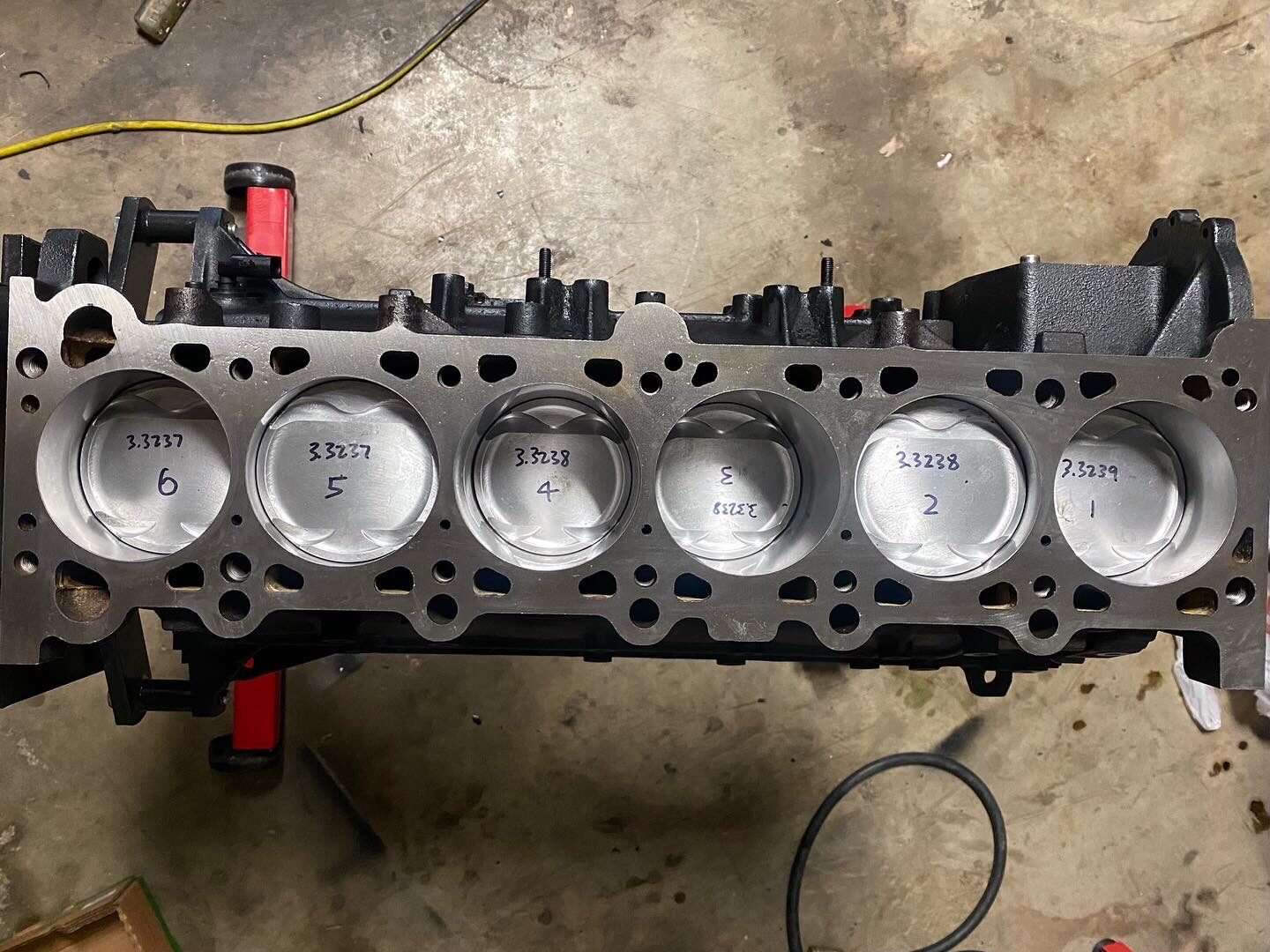
Head
When addressing the cylinder head, my choice led me to commence with an M50 Non-Vanos head. This was primarily due to its factory dual valve springs, which can be reliably revved up to 8500 RPM. Recognizing the significance of Vanos— variable valve timing for the intake camshaft—in enhancing engine responsiveness, I decided to modify the head to incorporate Vanos. To complement this, I matched the head with a set of M3 camshafts sourced from an S52 engine. These camshafts were degreed to fine-tune the camshaft timing, resulting in a strategic shift of the powerband to an optimal position.
Given that the engine would be turbocharged, the connection between the head and the block requires enhanced strength. To address this, I utilized ARP2000 head bolts in conjunction with a Cutting Ring head gasket from Athena. This combined approach significantly increases the clamping force exerted between the cylinder head and the engine block, to ensure the head does not lift off the block.
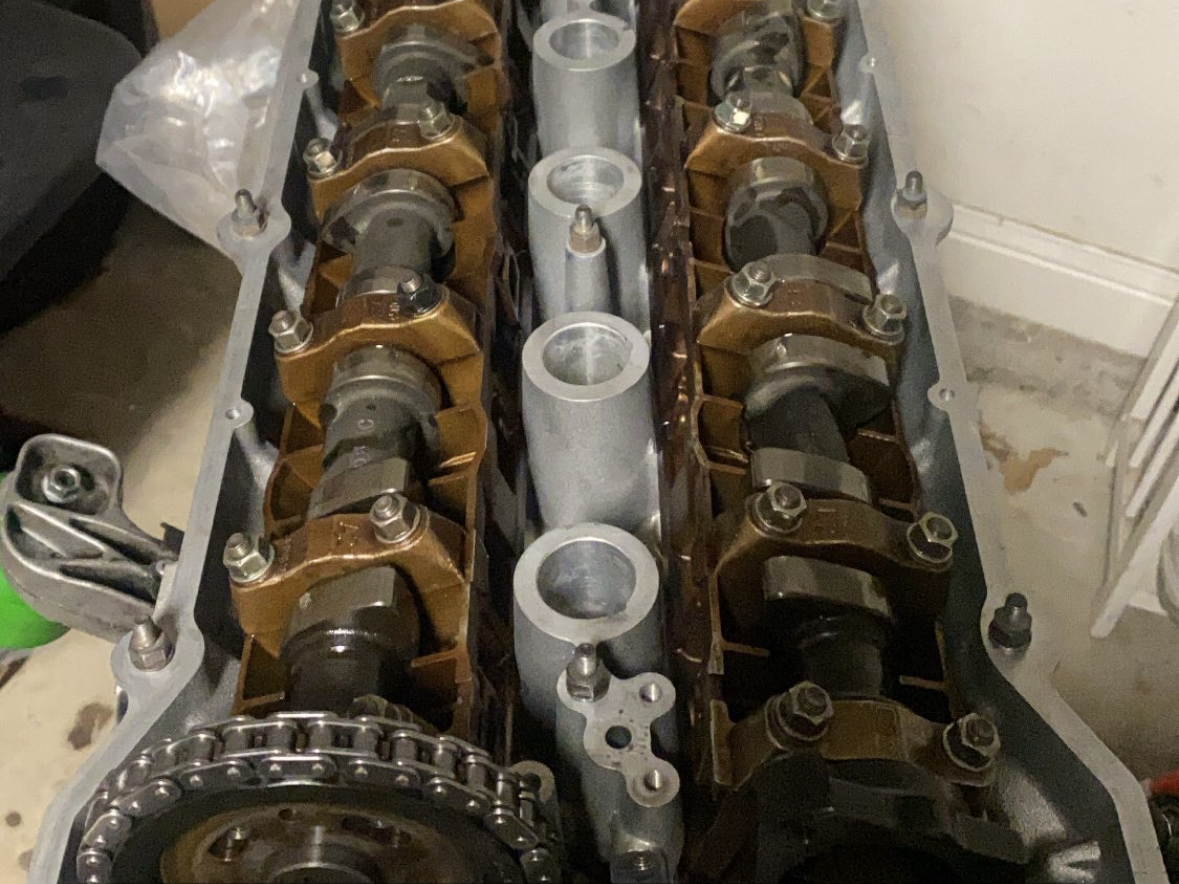
Turbocharger System
The hot side of the engine encompasses components such as the exhaust manifold, the turbocharger, exhaust piping, and turbo accessories. In terms of the exhaust manifold, I opted for a tubular manifold for a T4-sized turbo, accompanied by a 60mm wastegate designed to control the turbo’s boost. Considering my horsepower targets, I made a choice to go with a Precision 6466 Turbo. This selection was due to its impressive efficiency for my power goals with a street-oriented vehicle, having the perfect balance of power and response. This turbocharger was paired with a full 3” exhaust system, and there’s even the possibility of future upgrading to a 3.5” system if backpressure gets too high.
The cold side of the engine encompasses the intercooler piping system and the intake manifold. In terms of the intercooler, I opted for the largest size feasible within the confines of the E36 chassis. My choice was the Treadstone TR1245R, given my Texan location where hot summers are the norm. My intention was to ensure the reduction of intake air temperatures as much as possible in order to optimize combustion efficiency. To mount this intercooler, I designed custom brackets, as no ready-made solutions were available. Prior to the intercooler, I used 2.5” intercooler piping, while after the intercooler to the throttle body I used 3” piping.
As part of the setup, I integrated an HKS blow-off valve, which effectively releases pressure from the system upon throttle closure. Despite the turbo I’ve installed featuring an anti-surge mechanism, the inclusion of the blow-off valve prolongs the turbo’s lifespan. Moreover, it ensures consistent turbo spooling, enhancing engine response during throttle transitions.
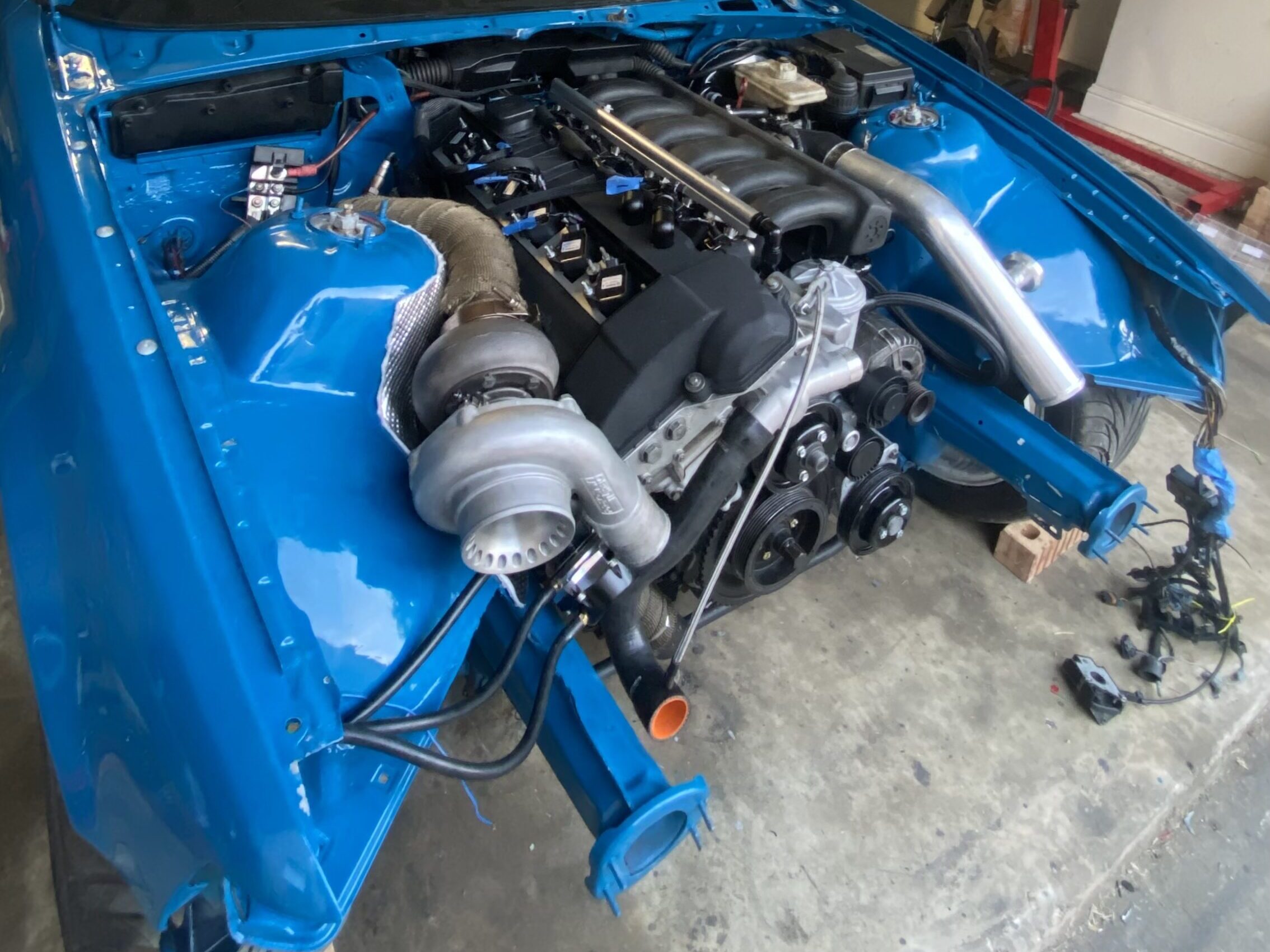
Additional Systems
Cooling System
Given the heat generated by the turbocharger and the higher temperatures within the engine bay, enhancing the cooling system was a vital step for ensuring reliability and optimal engine health. Since the car is in Texas, I decided to delete the heater core by blocking off the port on the back of the head. This actually increases cooling efficiency by forcing cooler coolant to circulate throughout the entire head, rather than remaining confined to one side of the engine.
Furthermore, I executed an OEM+ upgrade by replacing the radiator with a thicker one sourced from a BMW Z3M. This switch provides an increased coolant capacity and cooling surface. To ensure adequate airflow through the radiator, I transitioned from a clutch-type fan to a dual push-pull electric fan configuration, increasing the airflow rate.
In the pursuit of cooling efficiency, I also upgraded from a water pump equipped with a plastic impeller to one featuring a metal impeller. This upgrade has double the efficiency and a 15% increase in flow rate, contributing significantly to the overall cooling performance.
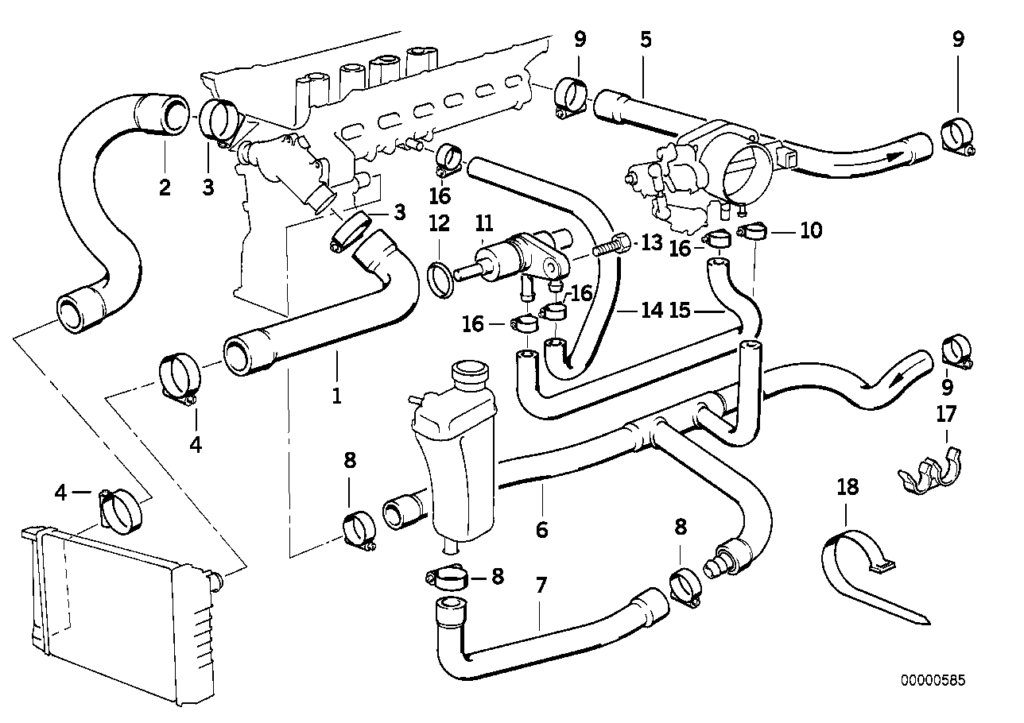
Fuel System
The fuel system plays a critical role in ensuring proper engine operation. This system encompasses various components, including the fuel pumps, fuel lines, fuel injectors, fuel pressure regulator, and ethanol content sensor. In the realm of fuel pumps, I made the decision to upgrade to dual Walbro 450s, in order to maintain consistent pressure within the lines. Recognizing that ethanol content can adversely affect factory rubber lines, I used larger PTFE AN lines as replacements. Given my power target of 800hp, I selected 1200CC injectors, which deliver more than enough fuel flow for that output.
For the fuel pressure regulator, I went with a Deatschwerks DWR1000, due to its proven reliability across numerous high-horsepower vehicles. To facilitate the utilization of flex fuel, I added an ethanol content sensor, providing real-time readings, allowing the tune to autonomously adjust during driving based on ethanol content fluctuations.
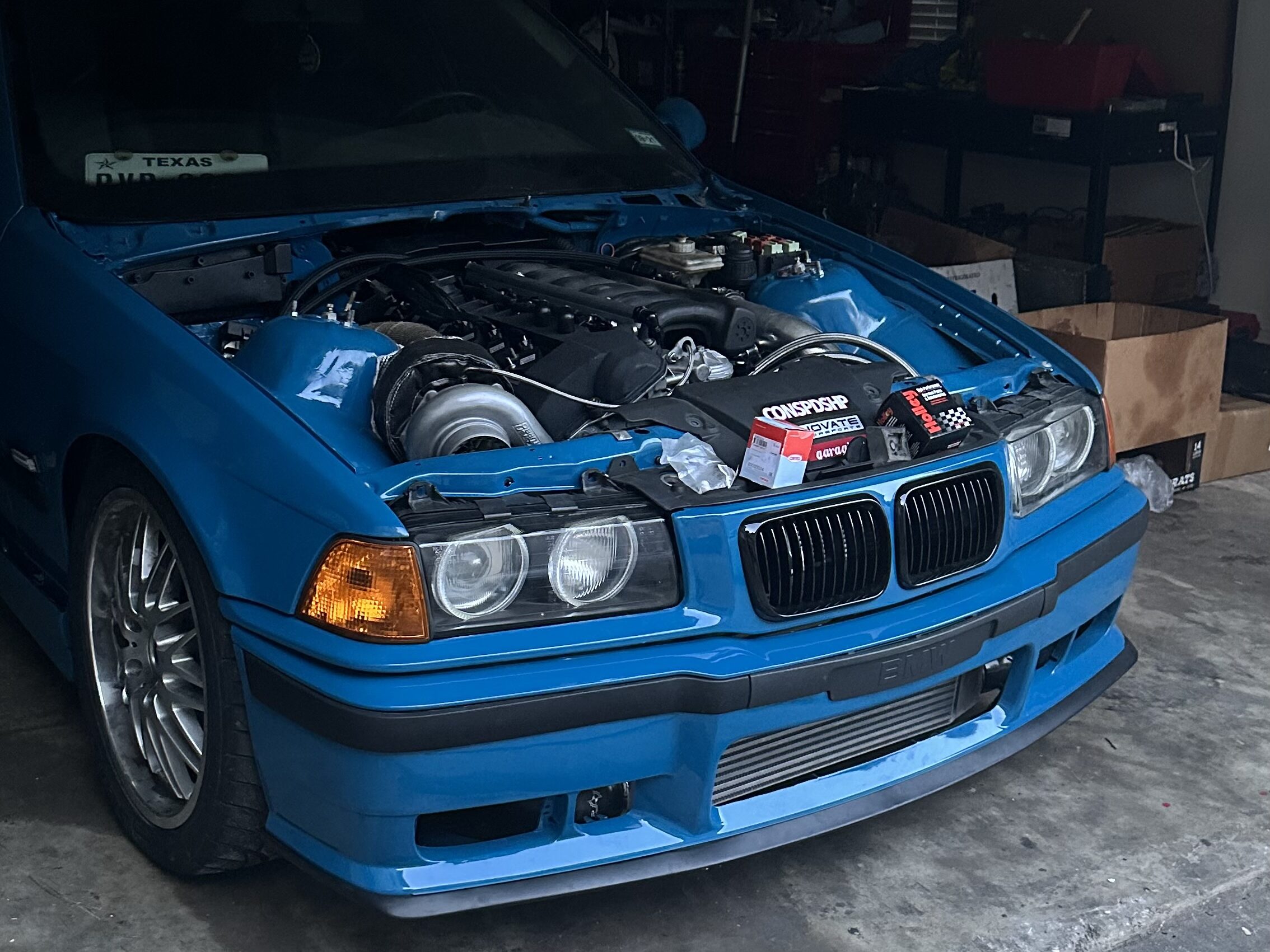
Ignition System
Since this was a 25+ year old car, it was the perfect opportunity to upgrade the coil packs. After extensive research, I found that coil packs from a newer BMW engine, specifically the B58, would be the best option. These newer coil packs delivered a stronger spark, are significantly cheaper, and were readily available compared to the stock coil packs. However, a challenge arose: no one had used B58 coil packs on an M50/52 engine before.
After learning about their similarities and differences from the stock coil packs, I engineered a conversion kit that could seamlessly integrate these upgraded coil packs into E36 and E46 engines. This product led me to start my company, Tuner Tech LLC. The conversion solution is not only cost-effective but also addresses challenges encountered by various high-horsepower builds.
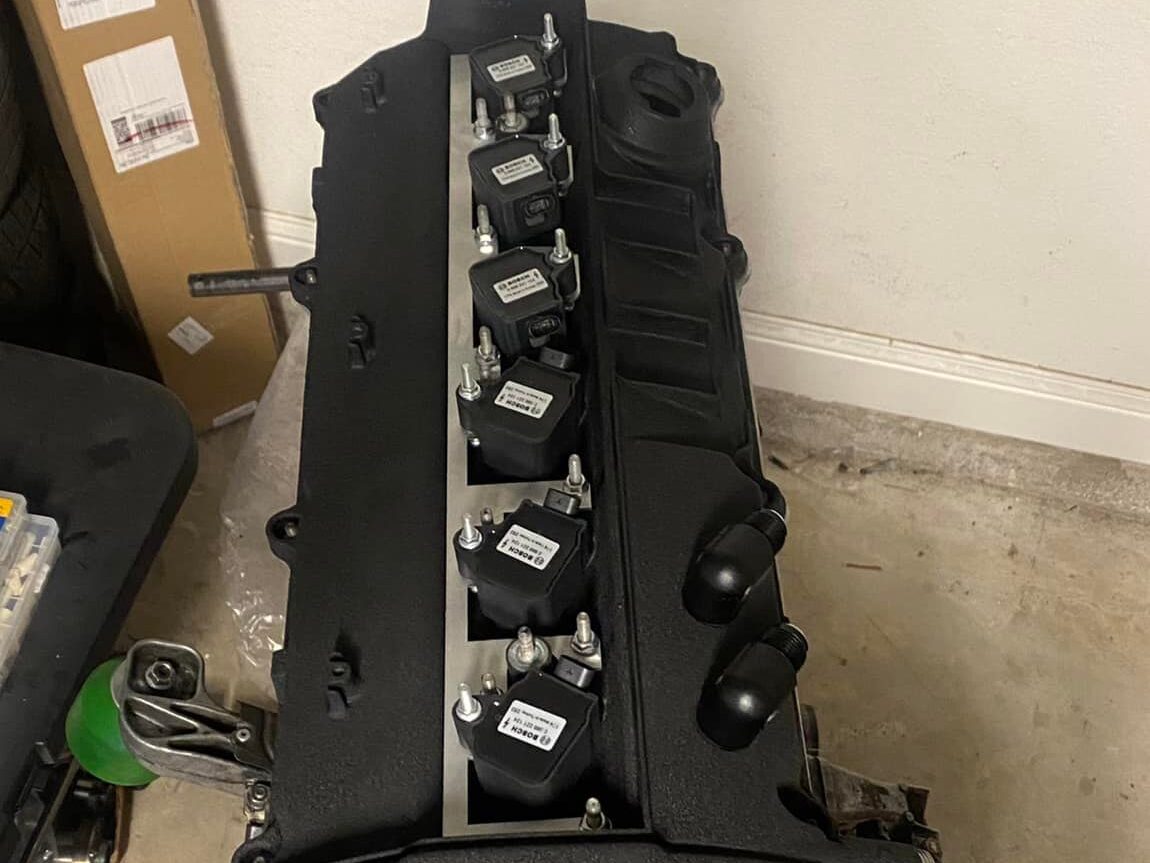